Rotary Kiln Direct Firing: Advanced Solutions for Efficient Industrial Heating
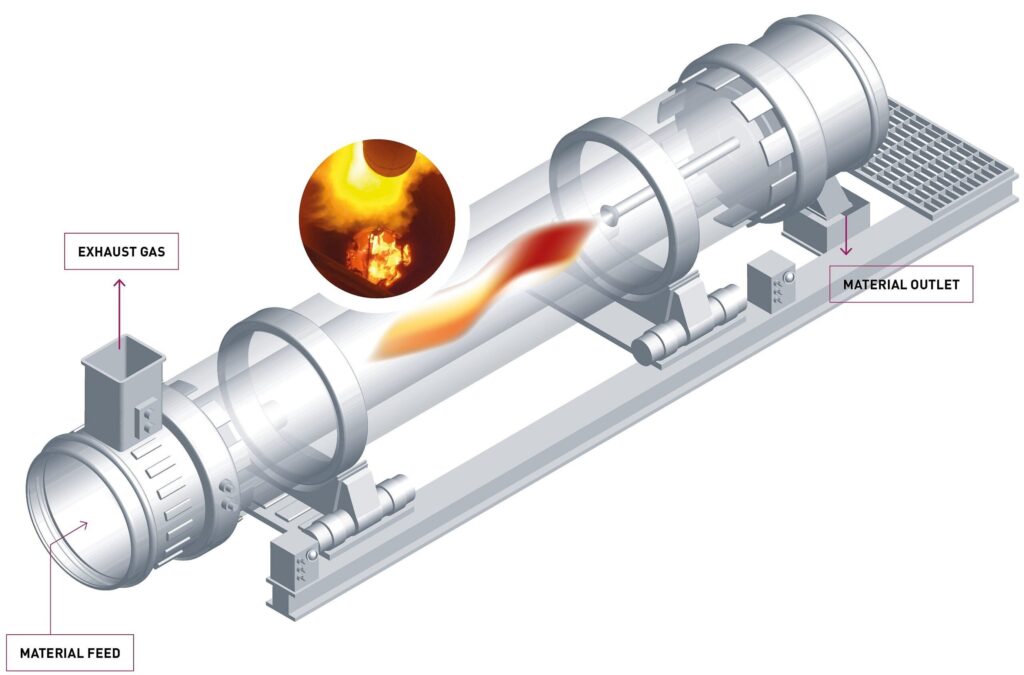
What is Rotary Kiln Direct Firing?
Rotary kiln direct firing is a method where fuel is combusted directly inside the rotary kiln. This process involves injecting fuel—typically natural gas, oil, or pulverized coal—directly into the kiln’s combustion zone. The resulting high-temperature environment effectively heats the material being processed as the kiln rotates, facilitating various chemical and physical transformations.
Benefits of Rotary Kiln Direct Firing
- Enhanced Thermal Efficiency
Direct firing is renowned for its high thermal efficiency. By burning the fuel directly within the kiln, you achieve optimal heat transfer to the material, resulting in more effective processing and reduced energy consumption. This efficient heat transfer minimizes fuel usage and maximizes productivity. - Cost Savings
One of the most significant advantages of rotary kiln is its potential for cost savings. Reduced fuel consumption and lower operational expenses make this method a cost-effective solution. The simplified system design also reduces maintenance costs and operational complexities. - Superior Process Control
Rotary kiln direct firing provides precise control over combustion and temperature distribution. This control is crucial for achieving consistent product quality and ensuring that the materials are processed under optimal conditions. - Fuel Flexibility
Direct firing systems are versatile and can accommodate various fuels, including natural gas, oil, and coal. This flexibility allows you to select the most economical or available fuel for your specific needs, contributing to further cost savings.
Applications of Rotary Kiln Direct Firing
Rotary kiln is widely used across several industries:
- Cement Production: Essential for producing high-quality clinker, a key component in cement manufacturing. Direct firing ensures efficient and uniform heating, critical for clinker formation.
- Mineral Processing: Used for processing ores and minerals, including calcining limestone and roasting metals. The high temperatures facilitate the necessary chemical reactions and transformations.
- Chemical Manufacturing: Ideal for producing chemicals through high-temperature reactions, ensuring that the materials are heated uniformly for optimal results.
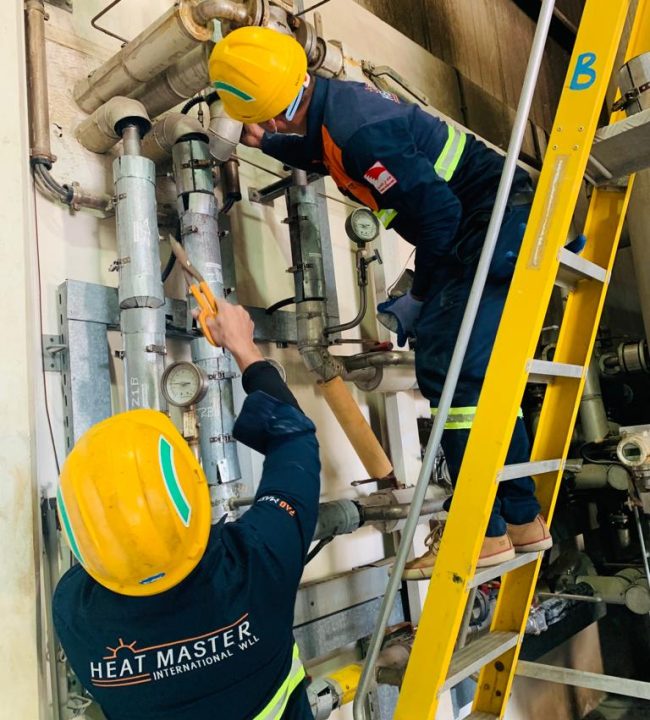
Maintenance and Safety
Maintaining a rotary kiln with direct firing involves:
- Routine Inspections: Regularly inspect the fuel injection system, kiln lining, and combustion zone to ensure proper operation and efficiency.
- Safety Protocols: Implement comprehensive safety measures for handling and storing fuels. Monitor emissions to ensure compliance with environmental regulations.
- Upgrades and Replacements: Periodically upgrade components such as burners or fuel injection systems to maintain optimal performance and efficiency.
Conclusion
Rotary kiln direct firing is a highly effective technology that enhances industrial heating processes with its efficiency, flexibility, and cost-effectiveness. By utilizing direct combustion within the kiln, you achieve superior heat transfer, reduced fuel consumption, and better process control, leading to improved product quality and lower operational costs.
For more information on integrating rotary kiln into your operations or to discuss how our solutions can meet your specific needs, contact us today. Our team of experts is ready to provide you with the guidance and support necessary to optimize your industrial processes.
For more details, Contact us
phone: +973 38456667
email: marketing@heatmasterint.com